LPKF Protolaser U3
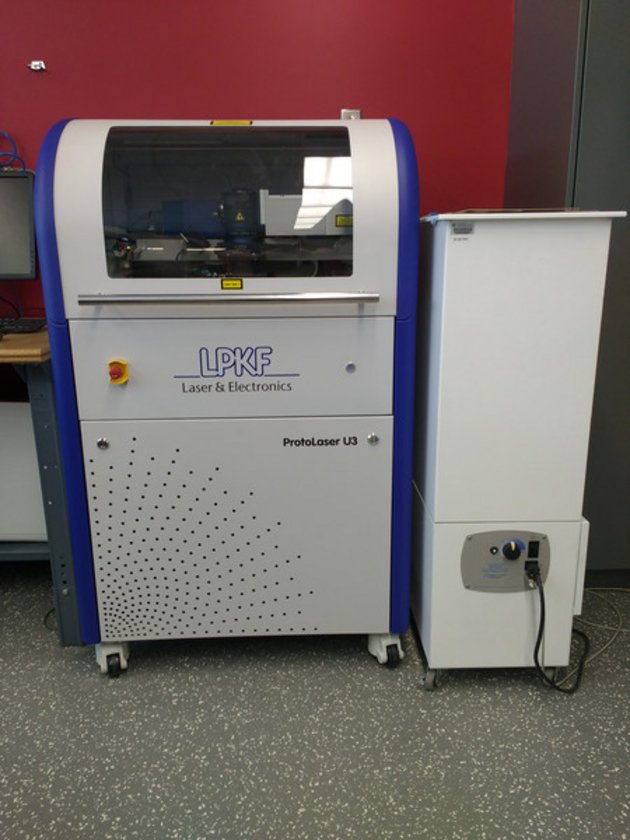
The LPKF Protolaser U3 is an automatic 2D/3D UV LASER engraving and cutting system for cutting, machining, selectively delaminating or simply heating or making a local UV exposure on a multitude of materials.
Cutting
The beam can cut materials up to 0.8 mm thick in a single pass. For thicker materials, several passes at various depths are recommended.
Machining
By adjusting the parameters of the LASER (scanning speed, power, frequency, number of successive passes) it is possible to engrave only part of the surface of the sample. This makes it possible to do 3D machining, as a milling machine would, or to remove a layer of material (example : copper) without damaging the underlying surface too much.
Delamination
In some cases, the device offers the possibility of simply delaminating material from an underlying layer. This greatly speeds up the process time while affecting the substrate surface less. In this case, the device cuts the material into thin strips and takes them off using a low-intensity LASER heater and an air jet.
Heating and selective UV exposure
At low intensity, the LASER can be used to make a local heat treatment to a sample. It is also possible to use UV properties to carry out surface treatments.
Supported file formats
The device, originally designed for the realization of double-sided printed circuit boards, can be used with gerber or DXF format files.
Specifications
Parameter | Value |
---|---|
Work surface | 9(22.9 cm) x 12 (30.5 cm) x 0.4 (1.0cm) |
Beam diameter at focus | 15 µm |
Minimum cutting width | 18 µm |
Max. table movement speed (X,Y) | 500 mm/sec |
Max. table movement speed (Z) | 20 mm/sec |
Maxi. beam scanning speed | 2000 mm/sec |
Precision on scan repetition | ±2 µm |
Source LASER | Diode-pumped YAG |
LASER Power | up to 6 W |
Wavelength | 355 nm |
Heartbeat frequency | 0-200 kHz |
Classification LASER | Class I (LASER in a closed case) |
- Automatic double-sided alignment on circular alignment marks or corners.
- Automatic/dynamic focus on the surface (Coming soon)
Cut or engraved materials
List of cut or engraved materials (list for example, not complete)
- Silicon: cuts up to more than 750 μm. Machining up to 100 μm (deeper is probably possible but machining at too much power seems to make the silicon amorphous under the machined area. A translucent amorphous layer is also formed on the machined surface (SiO2). This residue is removed by HF etching (BOE) if the sample permits. The use of an adhesive film on the sample avoids the majority of the residue and is easily removed in a solvent bath. An adhesive film under the sample is not recommended because it melts.
- Tungsten: cutting up to 500 μm. Untested machining.
- Pyrex waffle: cuts up to 200 μm. The Pyrex Amrid recipe has been adjusted specifically for these waffles. Untested machining.
- Soda glass file or glass strips: Cut up to 1 mm when cut double-sided. Machining possible, but recipe to be refined, because thermal shocks occur.
- PZT (Piezoelectric ceramic): Cutting up to 1 mm, Machining tested up to 200 μm deep. Thermal effect on polarization not tested.
- Black rubber: cut up to at least 3 mm. Rubbers that are too soft tend to re-seal the cut which can affect the cut.
- High Density Polyethylene (HDPE): very difficult cutting. The material diffuses the beam a lot and tends to melt rather than vaporize which deforms the surface without really cutting.
- Aluminum: cut up to 3/16 possible, but very long. Cut on thin sheets without too many problems. Untested machining.
- Epoxy (microchip style): Cutting on more than 1 mm, Machining on more than 500 μm.
- Polyimide cutting with FEP (Kapton FN): Cutting up to 127 μm. During precision cutting (so as not to affect the substrate on which the film is laid) the FEP layer under the Kapton melts and re-seals. Machining results in carbonization, not recommended or adjustment of the required recipe.
- Kapton: several thicknesses (2, 3, 5 mil) for creating stencils for spreading tin paste.
- FR4 : 11-2 layers (.5 oz copper and less). PCBS thicker than 32 mils are more difficult to cut.